La búsqueda constante de la excelencia operativa implica un continuo viaje hacia la mejora y la eficiencia. En el núcleo de este trayecto residen los principios fundamentales de la metodología KAIZEN™ y la estabilidad básica de la producción, los cuales constituyen los pilares de las operaciones de alto rendimiento. La metodología KAIZEN™ se centra en la mejora continua y la eliminación de desperdicios (Muda), ofreciendo una guía para identificar y eliminar obstáculos que afectan la eficiencia. Paralelamente, para lograr una transformación operativa exitosa, es crucial considerar también las 4 Ms de la estabilidad básica en las operaciones: métodos, máquinas, materiales y mano de obra. El análisis de cada uno de estos elementos es esencial para maximizar la productividad.
La integración de estas prácticas con estrategias de mejora continua permite un crecimiento sostenible y resiliente. En este artículo, exploraremos cómo estos principios se entrelazan para conformar la base de un sistema operativo de excelencia.
La importancia de la metodología KAIZEN™ para alcanzar la excelencia operacional
La metodología KAIZEN™, con énfasis en la mejora continua, juega un papel crucial en la conquista de la excelencia operacional. Este enfoque japonés, centrado en pequeños cambios incrementales, es esencial para la optimización constante de los procesos y sistemas dentro de una organización. El enfoque KAIZEN™ incentiva una cultura donde cuestionar el status quo es frecuente y donde todos los miembros de los equipos son alentados a contribuir con ideas de mejora.
La clave para el éxito al seguir los principios KAIZEN™ se basa en su aplicabilidad universal — pueden ser implementados en cualquier proceso, departamento o función, convirtiéndolos en una herramienta útil para alcanzar la excelencia operacional en todos los niveles de la organización. Al enfocarse en mejoras continuas, incluso si son pequeñas, las empresas pueden lograr ganancias significativas en eficiencia, productividad y calidad.
Este compromiso hacia la mejora continua va más allá de la simple optimización de los procesos; este compromiso está arraigado en la cultura organizacional, promoviendo un ambiente donde la innovación y la eficiencia son estimuladas. A través de la identificación y eliminación de desperdicios (Muda), la metodología KAIZEN™ contribuye a operaciones más lean y sostenibles.
A continuación, y con foco en la identificación proactiva y en la eliminación de ineficiencias se encuentran los principales tipos de Muda y cómo el reconocimiento de los mismos puede impulsar aún más la excelencia operacional.
Identificación de tipos y variables de Muda
En el contexto de la excelencia operacional, la identificación de los tipos de Muda es esencial para implementar efectivamente la filosofía KAIZEN™. Muda, el término japonés para desperdicio, se refiere a cualquier aspecto de un proceso que no añade valor. La identificación y eliminación de las Mudas son fundamentales para aumentar la eficiencia y reducir costes. A continuación, los 7 tipos de Muda y cómo identificarse y mitigarse en las operaciones:
- Producción en exceso: producir más de lo necesario o antes de lo necesario puede llevar al exceso de stocks, lo que aumenta los costes de almacenamiento y el riesgo de obsolescencia. El enfoque en la demanda real y la adopción de prácticas como el Just-In-Time pueden ayudar a minimizar este tipo de desperdicio.
- Personas en espera: cuando los empleados esperan por materiales, información o aprobaciones, el tiempo se desperdicia. La optimización del flujo de trabajo y la comunicación eficiente son fundamentales para reducir los tiempos de espera.
- Materiales e información en espera: similar al desperdicio anterior, la espera por materiales o información retrasa el proceso de producción. Sistemas de gestión eficaces y la sincronización de la cadena de suministro son cruciales para lidiar con este tipo de Muda.
- Movimiento de personas: movimientos innecesarios de empleados durante el trabajo pueden generar ineficiencias. La reorganización del espacio de trabajo para minimizar movimientos es una estrategia eficaz.
- Transporte de materiales y transferencia de información: el transporte excesivo de materiales y la transferencia innecesaria de información crean ineficiencias. Reducir estos movimientos a través del rediseño del layout de la fábrica o a través de sistemas de información integrados puede ser beneficioso.
- Sobreprocesamiento: realizar más trabajo o procedimientos más complejos de lo necesario puede ser una fuente de desperdicio. Simplificar procesos y asegurar que cada paso añade valor es primordial.
- Errores y defectos: errores y defectos resultan en retrabajo y en la insatisfacción del cliente. Implementar sistemas robustos de control de calidad y adoptar un enfoque de prevención puede ayudar a minimizar estos tipos de Mudas.
La identificación y el abordaje de estos tipos de desperdicios hacen que las organizaciones den pasos significativos hacia la excelencia operacional. Al proseguir con la eliminación de las Mudas es crucial involucrar grupos funcionales en ejercicios de sensibilización sobre los mismos, la denominada “caza a la Muda”, para que todos reconozcan sus variables y oportunidades de mejora.
Las variables críticas de Muda se refieren a indicadores mensurables de los factores que generan desperdicio. El objetivo de la involucración de estos grupos, es que estos sean desafiados con tareas de eliminación de desperdicio, para que comiencen a comprender y a aplicar cambios tangibles en los procesos operacionales.
Por ejemplo, la reducción del tiempo de cambio de máquinas (changeover time – CO) es una variable clásica de mejora lean y una variable crítica de Muda. El análisis minucioso del tiempo entre la última pieza de buena calidad de un lote y la primera del próximo puede revelar ineficiencias significativas. Tradicionalmente, el tiempo total de CO era visto como un parámetro fijo; sin embargo, con la mentalidad KAIZEN™, se comprendió que este tiempo puede y debe ser minimizado.
Al detallar las actividades durante el tiempo de cambio, a través de observación directa o análisis de vídeos, se pueden descubrir muchas oportunidades de mejora. Por ejemplo, la secuencia de tareas puede ser mejorada, al reducir movimientos innecesarios o esperas. La aproximación KAIZEN™ destaca así que el tiempo de cambio es una variable que puede ser optimizada con la debida identificación de los desperdicios e implementación de acciones de mejora.
Al enfocarse en la reducción del CO, por ejemplo, es posible involucrar a todos los operadores en un proceso de mejora continua, donde estos no solo ejecutarán tareas, sino también contribuirán a la identificación y resolución de ineficiencias. Este proceso colaborativo es un aspecto central de la filosofía KAIZEN™, que valora el conocimiento y la experiencia de todos los operarios.
Así, las variables críticas de Muda pueden ser el tiempo que un operario tarda en ejecutar una tarea (involucrado en cualquier tarea de producción, logística o administrativa), el número de piezas con defecto o la cantidad de inventario (es decir, la cantidad de materiales esperando en un punto dado).
Los indicadores mensurables de las variables críticas de Muda proporcionan un medio para la evaluación de la eficacia de los cambios implementados. Considerando el ejemplo anterior al medir el impacto de las mejoras en el tiempo de cambio, las organizaciones pueden ver no solo una reducción en el tiempo de inactividad, sino también mejoras en otros indicadores, como en la calidad del producto y en el tiempo de respuesta al cliente.
Además del CO, otros elementos críticos del flujo de producción deben ser analizados, como el WIP (work in process), el lead time y el tamaño del lote. El WIP y el lead time están directamente relacionados con la capacidad de una organización de responder rápidamente a la demanda de los clientes, mientras que el tamaño del lote afecta la flexibilidad y la capacidad de respuesta. Un enfoque de flujo unitario, que contrasta con la producción en lotes, puede ayudar a reducir el lead time y el WIP, aumentando así la agilidad y la eficiencia.
Dentro de un flujo de producción en pull, componentes como el lead time total son variables fundamentales. Reducir el lead time del flujo de información y de materiales es de esta forma crucial para la implementación efectiva de un sistema en pull, donde la producción se basa en la demanda real con el objetivo de minimizar el exceso de stocks y los desperdicios asociados.
Las acciones de mejora deben también considerar las tasas de disponibilidad de las máquinas, los niveles de servicio y tasas de defectos, que son vitales para la estabilidad básica de las operaciones, como veremos a continuación. La monitorización y la mejora de estos indicadores llevan a un ambiente de producción más predecible y fiable, donde los recursos son utilizados de forma optimizada, y los productos son entregados de forma consistente y con alta calidad.
Este análisis de las variables críticas de Muda enfatiza la necesidad de un enfoque holístico en la gestión operacional, donde cada aspecto del proceso es continuamente examinado y perfeccionado. El enfoque de estas variables contribuye así a la mejora de las operaciones y para alcanzar la estabilidad básica.
Las 4Ms de la estabilidad básica en las operaciones: los pilares de la reducción de desperdicio
La estabilidad básica en las operaciones es a menudo evaluada a través de las 4 Ms: mano de obra, máquinas, materiales y métodos. Estos elementos son considerados como pilares en la reducción del desperdicio y en la mejora continua de los procesos productivos. Identificar y analizar estos cuatro elementos es esencial para evitar interrupciones que puedan afectar el flujo y, como consecuencia, a la eficiencia operacional.
La mano de obra, la primera M, está intrínsecamente vinculada a la fiabilidad del sistema. La puntualidad y la presencia de los operadores son esenciales para mantener la consistencia y prevenir retrasos en la producción. A continuación, tenemos las máquinas, cuyas tasas de disponibilidad deben ser maximizadas para evitar períodos de inactividad no planificados que puedan interrumpir el flujo de las operaciones. En cuanto a los materiales, estos requieren especial atención debido a las tasas de ruptura de stock, los stocks deben ser gestionados de forma que se asegure una cadena de suministro fluida y responsiva. Por último, los métodos aplicados deben ser perfeccionados y estandarizados para maximizar la calidad y minimizar el retrabajo, lo que nos lleva a la variable crítica representada por las tasas de defecto.
La resistencia al cambio es también un obstáculo significativo que puede comprometer la estabilidad básica. Las organizaciones deben, por lo tanto, cultivar una cultura que no solo acepte, sino que busque la mejora continua y la adaptación a los nuevos métodos y prácticas.
Una de las metáforas del lean sobre la estabilidad básica se representa con un iceberg. Los problemas relacionados con las 4Ms están por debajo de la parte visible del iceberg, y son numerosos los problemas que pueden darse.
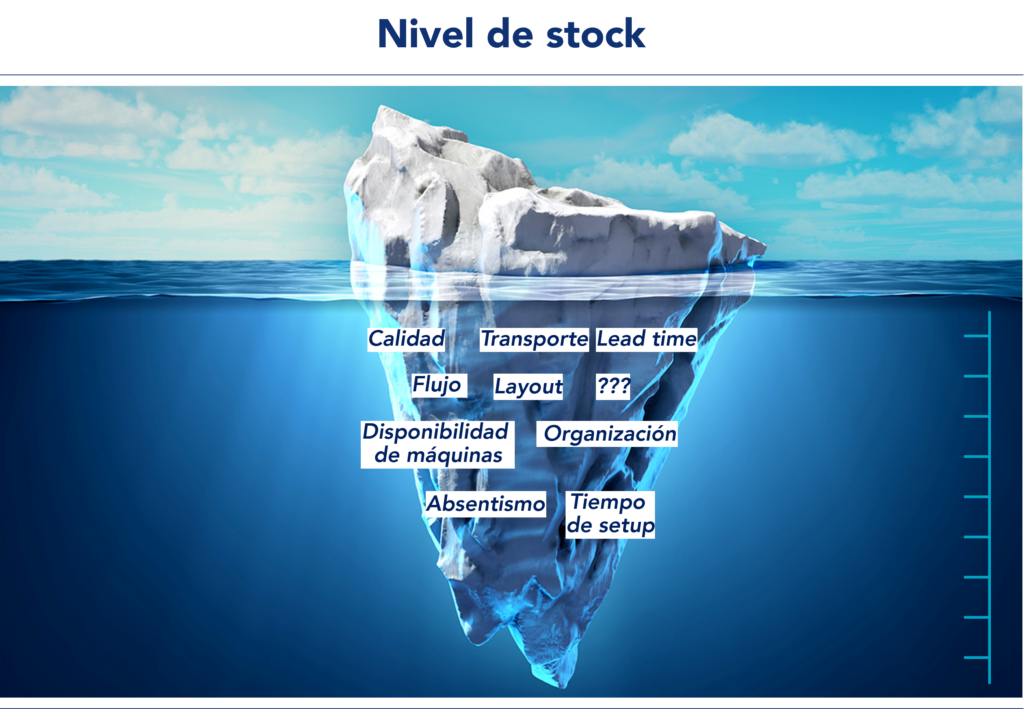
Siguiendo esta metáfora, la naturaleza exacta de estos problemas puede variar de empresa a empresa.
En este artículo abordamos la estabilidad básica, por lo que el foco se encuentra solo en las cuestiones que pueden causar problemas significativos si no se tratan desde el inicio. Algunos de ellos están relacionados con las siguientes variables críticas:
- Puntualidad y absentismo
- Tasas de disponibilidad de las máquinas
- Tasas de ruptura de stock de material
- Tasas de defectos de calidad
- Gran resistencia al cambio
A continuación, se encuentran con más detalle cada uno de las 4Ms.
Estabilidad básica de la mano de obra en las operaciones
La estabilidad de la mano de obra es un pilar para cualquier operación productiva, e identificar y gestionar las variables críticas de la mano de obra es esencial para asegurar la continuidad y la eficiencia de los procesos. La puntualidad y el absentismo de los operadores son variables críticas que requieren atención constante, pues impactan directamente la capacidad productiva y la estabilidad de las operaciones.
En esta óptica también la disciplina en el lugar de trabajo, especialmente en lo que respecta al cumplimiento de los horarios establecidos, es fundamental. Los operadores que inician sus tareas con retrasos o que hacen pausas más largas de lo estimado pueden generar retrasos significativos en la producción. Además, el absentismo no previsto puede interrumpir completamente las operaciones, creando cuellos de botella y afectando la entrega del producto final. Por lo tanto, es crucial implementar medidas que promuevan la asistencia y reduzcan las tasas de absentismo.
Para abordar estas cuestiones, es importante involucrar a los supervisores y al departamento de recursos humanos. Estos deben trabajar juntos para comprender las causas del absentismo e implementar estrategias para mitigarlo, como incentivos a la presencia o penalidades por faltas no justificadas. La definición de objetivos claros para la reducción del absentismo y la implementación de medidas para alcanzar estos objetivos son pasos importantes para mejorar la estabilidad de la mano de obra.
La herramienta SDCA (Standardize, Do, Check, Act) es muy útil en el contexto de la estabilidad de la mano de obra. Esta comienza por la estandarización, al crear una norma que resuelva un problema específico, pasando por la ejecución del trabajo conforme a la norma establecida, verificando y actuando en caso de desviaciones. Este ciclo es un enfoque sistemático para asegurar que las normas se mantienen y mejoran continuamente.
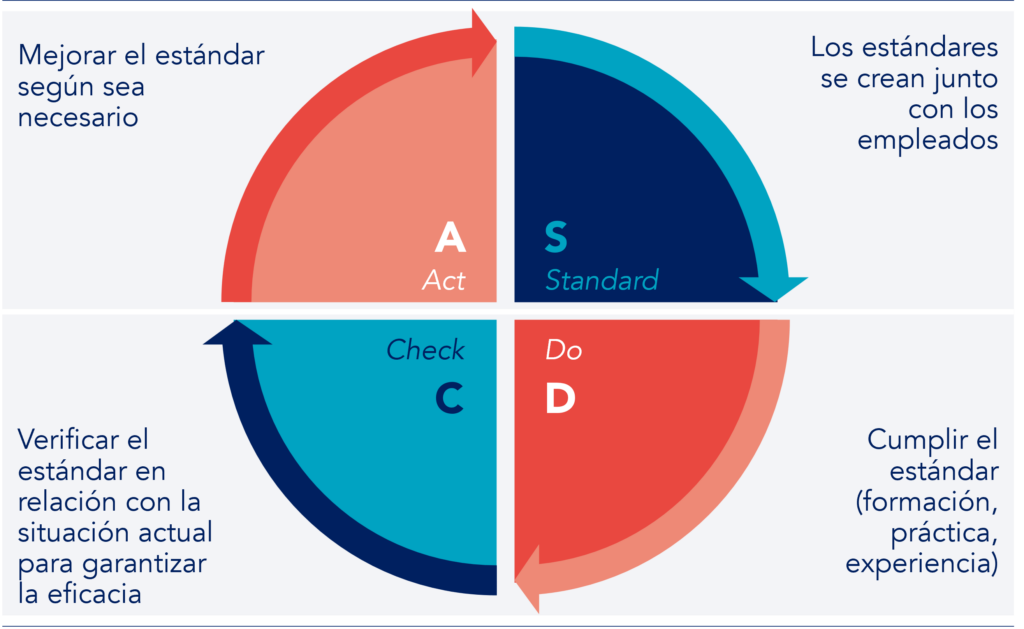
También la formación y las instrucciones de trabajo desempeñan un papel importante en la implementación de nuevas normas y en la garantía de que los operadores comprendan las expectativas y los procedimientos necesarios. Con la formación adecuada, los operadores estarán más capacitados para realizar sus tareas de forma eficaz, aumentando la productividad y reduciendo la probabilidad de errores.
A través del análisis y mejora continua de las variables críticas de la mano de obra, las empresas pueden alcanzar una mayor estabilidad en sus operaciones, creando un ambiente de trabajo que soporta el flujo constante y eficiente de producción, fundamental para la sostenibilidad y el crecimiento a largo plazo.
Estabilidad básica de las máquinas: reducir los tiempos de parada y aumentar la productividad
Las pérdidas de disponibilidad son a menudo el problema principal, con paradas inesperadas o averías que pueden tener un gran impacto en la estabilidad de las máquinas. Un índice de disponibilidad del 80% o más es generalmente considerado suficiente para iniciar un proyecto de flujo. Sin embargo, no es solo la media de disponibilidad lo que importa, sino también la variabilidad alrededor de esa media, conocida como desviación estándar, que puede ser un gran obstáculo para el flujo eficiente del proceso.
Aumentar el OEE requiere acciones específicas, especialmente en las máquinas que son consideradas como pacemaker (marcapasos) del sistema de logística en pull. Estas son máquinas que definen la capacidad de toda la cadena de logística y son esenciales para la programación de la producción.
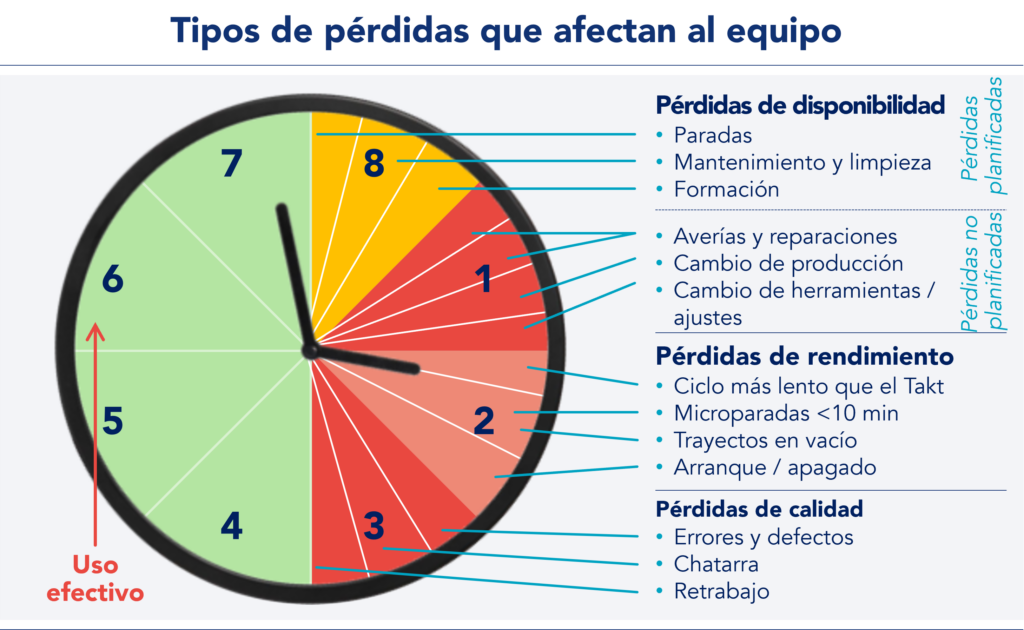
Los talleres Gemba Kaizen son una estrategia eficaz para abordar las pérdidas significativas y comenzar a resolver los problemas más críticos. Un análisis detallado de las causas de las averías, utilizando técnicas como los 5 Porqués o el diagrama de Ishikawa, es fundamental para comprender las raíces de los problemas y desarrollar medidas correctivas adecuadas.
Para resolver las cuestiones de estabilidad de las máquinas, es esencial formar grupos dedicados que incluyan representantes del departamento de mantenimiento y, para abordar los defectos, que involucren también operadores y supervisores de la producción y secciones de control de calidad.
Al trabajar estas cuestiones e implementar estándares eficaces de gestión visual y el ciclo SDCA, las organizaciones pueden resolver muchos problemas relacionados con la estabilidad de la mano de obra y equipos, lo que permite un flujo de trabajo más fiable y una mayor productividad.
Estabilidad básica de los materiales: racionalizar el inventario para optimizar el flujo
La falta de piezas o de materias primas esenciales o la inestabilidad de los proveedores que fallan o retrasan las entregas, pueden causar retrasos significativos y paradas en la producción.
La aplicación de los principios de la estabilidad al flujo de materiales revela que, cuando el nivel de rupturas de stock es bajo o el servicio de proveedores no es suficientemente robusto, puede ser necesario crear unos márgenes de inventario para asegurar la continuidad del flujo de materiales. Al inicio de un proyecto de flujo en pull, es importante identificar y resolver las grandes cuestiones relacionadas con la falta de materiales. El equipo de mejora enfocado en esta área generalmente incluye los departamentos de planificación y logística, que son responsables por el pedido de los materiales y por su gestión hasta su punto de uso.
En muchos casos, solo un cambio de sistema puede resolver problemas crónicos de suministro. Utilizando una lista de los principales problemas relacionados con materiales y aplicando el ciclo PDCA (Planificar, Hacer, Verificar, Actuar) de mejora, se pueden alcanzar resultados rápidos y eficaces.
Se aconseja que, al lidiar con los desafíos de la cadena de suministro y logística, las soluciones del modelo de Total Flow Management (TFM) sean consideradas, pues pueden resolver la mayoría de los problemas de suministro de material. Sin embargo, es fundamental ser realista al evaluar si una cuestión específica de estabilidad de material merece ser abordada, pues no todos los problemas serán solucionados con el mismo enfoque.
La experiencia de Kaizen Institute indica que, muchas veces, es mejor crear un sistema de resolución de problemas que trate con las causas más comunes de interrupciones en el suministro, lo que eventualmente resolverá la mayoría de los problemas y solucionará otros en paralelo. También es una buena práctica verificar regularmente la presencia de problemas de entrega con los proveedores o dentro de los procesos logísticos internos y externos, para garantizar la continuidad del flujo de materiales y la estabilidad operacional.
Estabilidad básica de los métodos: identificar y eliminar sistemáticamente el desperdicio
La estabilidad de los métodos en operaciones industriales se encuentra intrínsecamente ligada a la capacidad de mantener el flujo continuo de materiales e información, minimizando los buffers de seguridad y promoviendo un flujo preciso y eficiente. Problemas en la estabilidad de los métodos pueden manifestarse de diversas formas, pero frecuentemente están relacionados con restricciones de calidad y tiempo.
Un problema de estabilidad de métodos puede tener un impacto severo si ocurre de forma variable, es decir, con grandes variaciones alrededor de la media, lo que hace estos problemas impredecibles y capaces de parar una línea de producción entera. Estos problemas pueden no estar directamente ligados a una máquina específica (lo que estaría reflejado en el OEE de la máquina), sino ser un problema aleatorio con implicaciones en toda la cadena del proceso.
En este ámbito, si se considera la introducción de un nuevo producto esto requerirá una evaluación cuidadosa de la estabilidad de los métodos existentes. Mezclar una solución de flujo con la definición de los mejores parámetros para un nuevo proceso, puede no ser ideal para iniciar proyectos de flujo en pull, pues exige una consideración extra y discusiones detalladas para alinear ambos objetivos.
La mejor forma de iniciar un proyecto de flujo en pull es con un proceso que esté estable y sea fiable en términos de mano de obra, máquinas, materiales y métodos.
Aun así, en un escenario donde ningún nuevo producto está siendo introducido y donde no hay cambios significativos en los procesos en curso, es prudente verificar siempre la estabilidad de los métodos antes de iniciar un proyecto de este tipo. Esto puede hacerse al identificar cualquier problema mayor relacionado con tiempos, calidad, seguridad o ergonomía, y realizando talleres Gemba Kaizen con grupos dedicados.
Estos talleres son una oportunidad para analizar sistemáticamente los métodos actuales, identificar las fuentes de desperdicio y trabajar colaborativamente para desarrollar soluciones que mejoren la estabilidad y eficiencia de los procesos. Con la aplicación consistente de prácticas de mejora continua y con la eliminación del desperdicio, las operaciones pueden alcanzar un nivel de estabilidad que sostenga una productividad elevada y una calidad consistente del producto.
Más sobre estabilidad de la mano de obra: capacitar a los empleados para operaciones lean
A menudo, el principal obstáculo para la estabilidad básica es la resistencia al cambio por parte de todos los involucrados — operadores, gestión intermedia y de alto nivel. Esta resistencia puede manifestarse a través de una reacción defensiva a cualquier propuesta de cambio, destacando obstáculos potenciales y excusas. Para superar esta resistencia, es esencial identificar y comprender sus raíces, que a menudo se encuentran en hábitos profundamente arraigados y en la reluctancia a desviarse de prácticas largamente establecidas.
Implementar cambios de forma gradual e involucrar a los empleados en el proceso puede ser una estrategia eficaz. Empezar en un área piloto o mejorar una operación más compleja puede demostrar el valor del cambio y ayudar a cambiar la mentalidad de los empleados. El enfoque 5S, así denominado por las iniciales de las palabras japonesas Seiri (clasificar), Seiton (ordenar), Seiso (limpiar), Seiketsu (estandarizar) y Shitsuke (sostener), es una herramienta poderosa en este proceso, que introduce cambios incrementales que pueden llevar a ganancias significativas en productividad y reducción de errores.
Al promover la estabilidad de la mano de obra, es importante abordar no solo los aspectos físicos del trabajo, sino también los psicológicos y culturales. Estimular la adhesión a los principios KAIZEN™ y de mejora continua requiere un esfuerzo planificado de formación e involucración en todos los niveles de la organización. La aceptación y el compromiso con los principios KAIZEN™ de flujo en pull son esenciales para implementar cambios sostenibles.
Algunas empresas denominan esta aproximación como la promoción de un sistema de gestión lean o la promoción del pensamiento lean. El desarrollo de una mentalidad de mejora continua y de la capacidad de cambio involucra la discusión y el ensayo de nuevas ideas, a menudo a través de Eventos KAIZEN™, donde los empleados se involucran directamente en el diseño de soluciones a problemas.
Antes de dar cualquier paso hacia la mejora del flujo en una organización, es crucial evaluar la estabilidad básica humana y definir medidas para su mejora. Esto prepara el terreno para una implementación exitosa de sistemas de producción lean y crea un ambiente donde las operaciones no son solo más eficientes, sino también donde los empleados se sienten empoderados y parte integral del proceso de mejora continua.
Integración de la mejora continua y las 4Ms para un crecimiento sostenible
La integración de la mejora continua con las 4Ms — mano de obra, máquinas, materiales y métodos — es esencial para un crecimiento sostenible en las empresas. La filosofía KAIZEN™, con su enfoque en mejoras incrementales y sistemáticas, sirve de fundamento para esta aproximación holística.
La sinergia entre la mejora continua, prácticas KAIZEN™ y las 4Ms resulta en una estructura operacional que no solo se adapta y mejora en respuesta a los cambios del mercado, sino que también prospera, asegurando un crecimiento sostenible y competitivo en el contexto dinámico actual.
A medida que las organizaciones evolucionan, afrentan desafíos y oportunidades que requieren respuestas rápidas e innovadoras. Al aplicar la filosofía KAIZEN™ de manera sistemática, la capacidad de responder con flexibilidad a tales desafíos se convierte en una competencia central.
De este modo, las empresas pueden transformar los desafíos en ventajas competitivas, asegurando que el crecimiento se logre no solo a través de la eficiencia operacional, sino también a través de la evolución de los modelos de negocio y de la creación de valor adicional para clientes y stakeholders.
La adaptación y el crecimiento no se basan solo en la optimización de lo ya conocido, sino también en la exploración de lo que aún puede ser descubierto y mejorado.
Estrategias para la identificación y eliminación continua de desperdicio
Para la identificación y eliminación continua de desperdicio, las empresas pueden adoptar varias herramientas y estrategias efectivas dentro del ámbito de su mejora continua:
- Mapeo del Flujo de Valor — VSM: esta técnica se utiliza para visualizar los flujos de materiales e información necesarios para llevar un producto o servicio hasta el cliente. El VSM ayuda a identificar dónde se agrega valor en los procesos y dónde ocurre el desperdicio, proporcionando una base sólida para las mejoras.
- Gemba Walks: esta práctica implica visitar el lugar de trabajo, donde se realiza el trabajo, para observar los procesos de primera mano. Este método permite identificar problemas y oportunidades de mejora desde una perspectiva directa y práctica.
- Diagrama de Ishikawa (Causa y Efecto): también conocido como diagrama de espina de pescado, se utiliza para rastrear las causas raíz de un problema específico o fallo en la calidad, llevando a una mejor comprensión de cómo eliminar determinado desperdicio.
- Trabajo Estándar: establece procedimientos claros y consistentes para cada operación y asegura que las tareas se ejecutan de manera eficiente y efectiva, minimizando la variabilidad y el desperdicio.
- Sistemas en pull: en contraste con los sistemas tradicionales push, los sistemas en pull aseguran que los productos se producen solo en respuesta a la demanda real, lo que ayuda a reducir la producción excesiva y el inventario innecesario.
Estas estrategias, cuando se integran en un marco de mejora continua, permiten a las empresas crear un ciclo virtuoso de evaluación, acción y reevaluación, conduciendo a operaciones más lean y a un crecimiento sostenido.
¿Aún tienes algunas dudas sobre KAIZEN™ y los principios de estabilidad?
¿Qué es la filosofía KAIZEN™?
KAIZEN™ es una palabra japonesa que significa «cambio para mejor» o «mejora continua». Este concepto es una filosofía aplicada a la gestión lean enfocada en la mejora continua de los procesos en todos los niveles de una organización, involucrando a todos los empleados. Esta metodología se caracteriza por pequeños cambios incrementales realizados de forma regular, en lugar de grandes transformaciones puntuales. El objetivo es optimizar los flujos de trabajo, reducir el desperdicio y aumentar la eficiencia y la productividad.
¿Qué son las 4Ms?
Las 4Ms de la estabilidad básica representan los siguientes elementos: Mano de Obra, Máquinas, Materiales y Métodos, y son los pilares fundamentales en muchos sistemas de producción y gestión de la calidad. Dentro de la filosofía de producción lean y KAIZEN™, las 4Ms son aspectos críticos que deben ser analizados y optimizados para garantizar eficiencia y calidad. A través de la mejora continua en estas áreas, una organización puede reducir errores, mejorar la seguridad en el trabajo y aumentar la satisfacción del cliente.
¿Qué es la producción lean?
Un sistema de producción lean (o manufactura esbelta) es una metodología que busca minimizar el desperdicio dentro de un sistema de producción sin comprometer la productividad. Esta metodología puede aplicarse en diversos sectores y no solo en la producción. La idea es crear más valor para los clientes con menos recursos, identificando y eliminando desperdicios en los procesos, como la producción excesiva, o tiempos de espera y defectos, a través de la implementación de sistemas en pull, y de herramientas, por ejemplo, como el Trabajo Estándar.
o