El Mantenimiento Autónomo, como pilar fundamental del TPM (Total Productive Maintenance), tiene como objetivo comprometer a los operarios de producción en la conservación y mantenimiento de los equipos. Este enfoque conduce a una mayor confiabilidad de los equipos, disminución de fallos, prolongación de la vida útil, reducción de tiempos de inactividad y mejora general del rendimiento operativo.
Introducción al Mantenimiento Productivo Total (TPM)
El TPM tuvo su origen en Japón, específicamente en la industria automovilística. Fue desarrollado por el Japan Institute of Plant Maintenance (JIPM) a principios de la década de 1970 y la aproximación a este concepto fue introducida inicialmente por la empresa Nippondenso, miembro del Grupo Toyota, como parte de las iniciativas para mejorar la eficiencia y fiabilidad de los equipos de producción.
El TPM es un enfoque integral de gestión y mantenimiento que tiene como objetivo lograr la máxima eficiencia del sistema de producción de una organización. Se basa en la participación activa de todos los miembros de la empresa, desde la alta dirección hasta los operarios de línea, con el propósito de eliminar pérdidas y optimizar la utilización de los recursos disponibles, como personas, procesos y equipos, sin necesidad de realizar inversiones significativas en nuevos activos.
El TPM busca la excelencia operacional, reduciendo el tiempo de inactividad, mejorando la calidad del producto, aumentando la productividad y maximizando la utilización de los recursos existentes. De hecho, el Mantenimiento Productivo Total va más allá del mantenimiento convencional, ya que involucra a todas las áreas de la organización en un esfuerzo conjunto para mejorar el rendimiento global.
El propósito del TPM es lograr la máxima eficiencia del sistema de producción mediante la eliminación de pérdidas. Estas pérdidas pueden incluir tiempos de parada no planificados, tiempos de configuración, retrabajo, defectos de calidad, baja velocidad, entre otros. El TPM busca identificar las fuentes de estas pérdidas e implementar medidas para eliminarlas, promoviendo la mejora continua y el aumento de la eficiencia operativa.
Al adoptar el Mantenimiento Productivo Total, las organizaciones buscan establecer una cultura de mantenimiento proactivo y responsabilidad compartida, capacitando a los operarios para desempeñar un papel activo en el mantenimiento y mejora de los equipos.
Los pilares del TPM
El TPM se basa en ocho pilares que son fundamentales para eliminar pérdidas. También contribuyen a promover la mejora continua en la organización.
1. Mantenimiento Autónomo:
El mantenimiento autónomo implica formar y responsabilizar a los operarios del mantenimiento básico y la inspección de los equipos. Se busca desarrollar una cultura de prevención en la que los operarios sean responsables de sus propios equipos. Actividades básicas como limpieza, inspección y lubricación simple son realizadas por los operarios para evitar el deterioro forzado.
2. Mejora Específica:
La mejora específica se refiere a las actividades dirigidas a la eliminación de pérdidas y mejora de procesos. Son actividades de grupos multifuncionales para mejorar los procesos y eliminar problemas crónicos, con el objetivo de aumentar el rendimiento de los equipos.
3. Mantenimiento Planificado:
El mantenimiento planificado tiene como objetivo maximizar la disponibilidad de los equipos mediante una planificación eficiente de las actividades de mantenimiento. Esto incluye la programación de inspecciones, mantenimientos preventivos y la gestión adecuada de los recursos necesarios. Es responsabilidad de los especialistas en mantenimiento.
4. Formación y Entrenamiento:
La formación de los operarios y otros empleados es fundamental para el éxito del TPM. Este pilar se centra en el desarrollo de habilidades técnicas y conocimiento de los empleados, proporcionando formación adecuada y promoviendo la concienciación sobre la importancia del TPM en todos los niveles de la organización.
5. Mantenimiento de la Calidad:
La calidad del producto está directamente relacionada con el rendimiento de los equipos. En este pilar, se implementan acciones para garantizar la calidad de los productos mediante mantenimientos preventivos, inspecciones rigurosas y análisis de datos para identificar problemas de calidad. Se busca establecer las condiciones para lograr «cero defectos».
6. EEM – Gestión Anticipada:
El EEM (Early Equipment Management) tiene como objetivo asegurar que las necesidades de mantenimiento se tengan en cuenta desde la etapa de diseño de los equipos. Este pilar promueve la colaboración entre los ingenieros de diseño y los equipos de mantenimiento y producción, con el fin de crear equipos fiables y fáciles de mantener.
7. Salud, Seguridad y Medio Ambiente:
La seguridad y la preservación del medio ambiente son aspectos esenciales en cualquier proceso de producción. Se enfoca en prácticas y políticas que garantizan la seguridad de los empleados y la preservación del medio ambiente, promoviendo un entorno de trabajo saludable y sostenible.
8. Sistemas de Apoyo Administrativo:
Este pilar establece sistemas y procesos administrativos eficientes que respaldan las actividades. Esto incluye la gestión de información y documentos, así como la integración de sistemas de mantenimiento con otras áreas de la organización.
¿Qué es el Mantenimiento Autónomo?
El Mantenimiento Autónomo (MA) es uno de los pilares fundamentales del TPM (Total Productive Maintenance) y tiene como objetivo involucrar a los operarios de producción en la conservación y mantenimiento de los equipos, creando una cultura de prevención en la que los operarios se convierten en los «dueños» de los equipos, siendo responsables de monitorizar sus condiciones operativas y garantizar el correcto funcionamiento.
La dirección de los talleres de MA debe ser responsabilidad del departamento de mantenimiento. Debe establecerse un equipo multidisciplinar de mejora en mantenimiento que incluya al responsable de producción, operarios de máquinas, el responsable de mantenimiento, operarios de mantenimiento y posiblemente miembros de calidad o del equipo de ingeniería. En el taller, es esencial aclarar quién será el equipo responsable de supervisar las condiciones operativas y la conservación de los equipos. Este equipo debe estar compuesto por al menos dos operarios, que serán los «dueños» de los equipos, quedando bajo su responsabilidad.
Las principales funciones de este equipo son:
Monitorizar las condiciones de funcionamiento:
El equipo de Mantenimiento autónomo debe realizar verificaciones «in situ» de los principales parámetros de los equipos. Esto implica observar el rendimiento, la operación y otros indicadores relevantes para garantizar su correcto funcionamiento. Los datos obtenidos deben registrarse y publicarse de acuerdo con las normas establecidas.
Realizar las tareas según las rutas estandarizadas:
El equipo debe seguir rutas estándar para llevar a cabo las tareas de mantenimiento autónomo. Estas rutas contienen instrucciones detalladas sobre las acciones a realizar, como limpieza, inspección, lubricación y otras actividades de mantenimiento preventivo. Es importante registrar e informar cualquier anomalía encontrada durante la ejecución de estas tareas.
Analizar e informar sobre los resultados:
El equipo de Mantenimiento Autónomo debe estar atento a desviaciones y anomalías en los equipos. En caso de que ocurran, deben analizar las causas de estas desviaciones y proponer soluciones adecuadas. Estos análisis son esenciales para identificar problemas recurrentes, implementar mejoras y evitar futuros fallos. Los resultados y análisis deben presentarse periódicamente según el calendario establecido por el área.
El Mantenimiento Autónomo permite que los operarios desempeñen un papel activo en la conservación y mantenimiento de los equipos, contribuyendo así a maximizar el rendimiento.
Beneficios del Mantenimiento Autónomo
El Mantenimiento Autónomo desempeña un papel crucial en el aumento de la eficiencia del sistema de producción. Al involucrar a los operarios en el cuidado y conservación de los equipos, se crea una mentalidad de prevención y responsabilidad compartida. Esto da como resultado una mayor fiabilidad de los equipos, reducción de fallos, aumento de la vida útil, reducción de los tiempos de inactividad y mejora general del rendimiento operativo. Más detalles de los beneficios del Mantenimiento Autónomo:
Mayor tiempo de actividad de los equipos
Con el Mantenimiento Autónomo, los operarios están capacitados para identificar problemas a tiempo, realizar actividades de mantenimiento preventivo y ejecutar tareas de rutina, como limpieza y lubricación. Esto resulta en una reducción de los tiempos de paro no planificados, aumentando el tiempo de actividad de los equipos.
Aumento de la vida útil de los equipos
Al involucrar a los operarios en el mantenimiento de los equipos, el MA contribuye al aumento de la vida útil de los activos. Los operarios están más atentos a las condiciones de funcionamiento, realizan inspecciones regulares y toman medidas para evitar el desgaste excesivo y los daños en los equipos.
Mejora en la calidad del producto
Al realizar actividades de limpieza e inspección, los operarios pueden identificar y corregir problemas que puedan afectar a la calidad. Esto resulta en una reducción de defectos y retrabajo, mejorando la calidad final del producto.
Mejor utilización de los recursos
Los operarios adquieren un mayor compromiso con los equipos y desarrollan un sentido de responsabilidad. Esto conduce a una mejor utilización de los recursos disponibles, como materiales, piezas de repuesto y tiempo de trabajo, evitando desperdicios y optimizando la eficiencia operativa. Los equipos de mantenimiento también quedan más libres para actividades técnicas con un mayor valor añadido, como mejoras técnicas, actividades avanzadas de prevención, mantenimiento planificado, análisis predictivo y resolución estructurada de problemas.
Mejora de la seguridad en el trabajo
El MA contribuye a crear un entorno de trabajo más seguro. Los operarios, al estar involucrados en las actividades de mantenimiento, son más conscientes de los riesgos y las medidas de seguridad necesarias. Esto resulta en una reducción de accidentes y lesiones relacionados con los equipos.
Mejora continua
El Mantenimiento Autónomo promueve una cultura de mejora continua. Los operarios están constantemente observando, analizando, diagnosticando equipos y proponiendo soluciones a los problemas y desviaciones identificados. Esto lleva a un ciclo de aprendizaje y mejora constante, impulsando la excelencia operacional.
Estos beneficios contribuyen a la eficiencia operativa, la reducción de costes y el fortalecimiento de la competitividad de las organizaciones.
Etapas para la Implementación del Mantenimiento Autónomo
El Mantenimiento Autónomo sigue un conjunto de siete etapas bien definidas. A continuación, destacamos la importancia de cada etapa y cómo contribuye a la excelencia operacional.
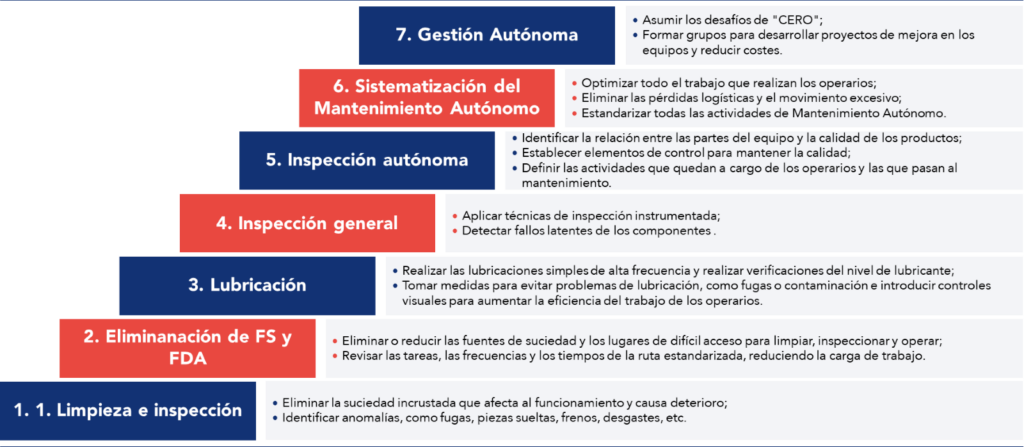
1. Limpieza e inspección
El primer paso del Mantenimiento Autónomo implica la limpieza e inspección de los equipos. El objetivo es que los operarios conozcan más y mejor los equipos que están operando y desarrollen el sentimiento de ser los «dueños» de los equipos.
Principales actividades a realizar:
- Eliminar la suciedad incrustada que afecta al funcionamiento y causa deterioro;
- Identificar anomalías, como fugas, piezas sueltas, frenos, desgastes, etc.
Objetivos para los equipos:
- Establecer las condiciones básicas de funcionamiento de los equipos;
- Exponer y tratar las anomalías ocultas;
- Prevenir el deterioro acelerado.
Papel de los líderes:
- Entrenar para reconocer qué son anomalías;
- Explicar la relación entre suciedad y deterioro acelerado;
- Enseñar el significado de inspeccionar mediante la limpieza;
- Mostrar las partes críticas de los equipos.
2. Eliminación de fuentes de suciedad (FS) y lugares de difícil acceso (LDA)
En esta etapa, los operarios buscan identificar y eliminar las fuentes de suciedad y las dificultades de acceso que pueden obstaculizar la limpieza e inspección adecuadas de los equipos. Los operarios deben aprender métodos simples para el análisis de problemas, elaborar «Lecciones de Un Punto» para pequeñas mejoras y participar en proyectos de mejora en grupo.
Principales actividades a realizar:
- Eliminar o reducir las fuentes de suciedad y los lugares de difícil acceso para limpiar, inspeccionar y operar (instalación de protecciones, mejora de los sistemas de recogida de residuos y otras acciones para hacer el mantenimiento más eficiente);
- Revisar las tareas, las frecuencias y los tiempos de la ruta estandarizada, reduciendo la carga de trabajo.
Objetivos para los equipos:
- Garantizar las condiciones de limpieza evitando la acumulación de suciedad;
- Mantener el control sobre las fuentes de suciedad, evitando que se propaguen;
- Aumentar la estabilidad, facilitando las inspecciones.
Papel de los líderes:
- Incentivar ideas de innovación y mostrar ejemplos;
- Enseñar métodos simples de análisis de problemas;
- Asegurar que el mantenimiento/proyecto responda con prontitud.
3. Lubricación
En este paso, los operarios aprenden a realizar la correcta lubricación de los puntos críticos de los equipos, siguiendo las especificaciones del fabricante. También son responsables de monitorizar los niveles de lubricante y tomar medidas para evitar problemas de lubricación, como fugas o contaminación. Los empleados deben comprender la importancia de los estándares para mantener las condiciones ideales de los equipos, entender para qué sirven los controles visuales y cómo utilizarlos.
Principales actividades a realizar:
- Realizar las lubricaciones simples de alta frecuencia;
- Realizar verificaciones del nivel de lubricante;
- Tomar medidas para evitar problemas de lubricación, como fugas o contaminación;
- Introducir controles visuales para aumentar la eficiencia del trabajo de los operarios.
Objetivos para los equipos:
- Restablecer las condiciones ideales de los equipos;
- Identificar en los propios equipos los puntos de limpieza, inspección y lubricación, así como los estándares que deben mantenerse.
Papel de los líderes:
- Definir las normas de lubricación y divulgarlas;
- Definir y estandarizar los modelos de controles visuales;
- Entrenar en técnicas de lubricación y elaborar las «Lecciones de Un Punto».
4. Inspección general
La inspección general es una etapa más amplia, en la cual los operarios realizan un análisis minucioso de los equipos. Verifican el desgaste, las holguras y otros signos de deterioro. Estas inspecciones ayudan a identificar problemas ocultos y tomar acciones preventivas antes de que se conviertan en fallos graves. Los empleados deben comprender la estructura de sus equipos formada por sistemas y funciones de los componentes, así como los criterios de inspección instrumentada y los modelos de control visual dinámico.
Principales actividades a realizar:
- Aplicar técnicas de inspección instrumentada;
- Detectar fallos latentes de los componentes que afectan sus funciones;
- Hacer uso extensivo de los controles visuales.
Objetivos para los equipos:
- Mejorar la confiabilidad a través de la inspección de los sistemas que componen el equipo;
- Adoptar controles visuales dinámicos como balanzas vibratorias, indicadores de flujo, etc.
Papel de los líderes:
- Preparar la sala de entrenamiento con los kits de materiales para cada sistema, mostrando los componentes en corte;
- Introducir el indicador y gráfico de fallas y anomalías por sistema.
5. Inspección autónoma
En este paso, los operarios están capacitados para realizar inspecciones más específicas en los equipos, utilizando herramientas y técnicas de inspección, como termografía, análisis de vibración, mediciones de presión, entre otras, para identificar problemas más sutiles y proporcionar información relevante para el mantenimiento. Los operarios deben comprender la relación entre los equipos y las cuestiones de calidad, profundizar y dominar los ajustes, estandarizar los procesos y realizar la sustitución de herramientas y dispositivos.
Principales actividades a realizar:
- Identificar la relación entre las partes del equipo y la calidad de los productos;
- Establecer elementos de control para mantener la calidad;
- Definir las actividades que quedan a cargo de los operarios y las que pasan al mantenimiento.
Objetivos para los equipos:
- Mejorar la capacidad de los equipos;
- Adoptar controles para dispositivos y herramientas a través de inspecciones específicas;
- Extender el uso de los controles visuales a los puntos relacionados con la calidad.
Papel de los líderes:
- Entrenar en los procedimientos de ajustes;
- Definir criterios claros para la división de responsabilidades entre Operación y Mantenimiento;
- Definir procedimientos de reposición para herramientas y dispositivos desgastados.
6. Sistematización del Mantenimiento Autónomo
La sistematización es una etapa esencial para garantizar que el Mantenimiento Autónomo se implemente de manera consistente y efectiva. Esto implica la creación de normas adecuadas para todas las actividades relacionadas con el Mantenimiento Autónomo. La sistematización facilita la estandarización, el entrenamiento y la transferencia de conocimientos entre los operarios. El objetivo es expandir la noción de organización del trabajo, enseñar a los empleados a elaborar procedimientos estandarizados e identificar las pérdidas logísticas en el propio trabajo.
Principales actividades a realizar:
- Optimizar todo el trabajo que realizan los operarios;
- Eliminar las pérdidas logísticas y el movimiento excesivo;
- Estandarizar todas las actividades de Mantenimiento Autónomo.
Objetivos para los equipos:
- Revisar la disposición de los equipos, la distribución de los materiales, dispositivos y herramientas auxiliares en el área de trabajo;
- Marcar/señalizar los lugares y pasillos, organizar los stocks e identificar las posiciones.
Papel de los líderes:
- Elaboración de procedimientos;
- Definir el mapeo del flujo de trabajo de los operarios;
- Entrenar en métodos de análisis de pérdidas y proyectos de mejora.
7. Gestión Autónoma
La gestión autónoma es la etapa final de los siete pasos del Mantenimiento Autónomo. En esta fase, los operarios asumen la responsabilidad completa de la gestión del proceso de Mantenimiento Autónomo. Desarrollan planes de acción, establecen metas, monitorizan los indicadores de desempeño y toman decisiones basadas en datos para garantizar la eficacia continua del Mantenimiento Autónomo. Los operarios deben aprender técnicas de gestión a través de datos de procesos e indicadores, deben comprender la relación entre los procesos y los costes operativos y aumentar sus habilidades para realizar intervenciones pequeñas.
Principales actividades a realizar:
- Asumir los desafíos de «CERO»;
- Tomar iniciativas para reducir costes;
- Formar grupos para desarrollar proyectos de mejora en los equipos;
- Sugerir metas para la gestión.
Objetivos para los equipos:
- Aumentar el ciclo de vida de los elementos críticos y puntos débiles;
- Automatizar algunas tareas con soluciones simples de bajo costo (lubricación centralizada);
- Instalar sensores para la recopilación de datos.
Papel de los líderes:
- Entrenar en cómo utilizar la gestión por objetivos;
- Entrenar en pequeñas intervenciones;
- Preparar y proporcionar información organizada y clasificada por relevancia sobre costes.
Los siete pasos del Mantenimiento Autónomo son fundamentales para crear una cultura de prevención y responsabilidad compartida en la conservación y mantenimiento de los equipos. Estos pasos guían a los operarios en actividades como limpieza, inspección, lubricación y análisis más avanzados. Siguiendo estos pasos de manera constante y sistemática, las organizaciones pueden lograr una mayor eficiencia operativa, una mayor vida útil de los equipos, una mejor calidad del producto y un entorno de trabajo más seguro.
Cuatro herramientas de apoyo para el Mantenimiento Autónomo
El Mantenimiento Autónomo utiliza herramientas de apoyo para su implementación, de las cuales destacamos cuatro: ruta estándar de tareas, etiquetas para identificación de problemas, lección de «un punto» y cuadro de actividades. Estas herramientas son fundamentales para el éxito del Mantenimiento Autónomo, ya que facilitan la organización, la comunicación y el registro de las actividades, promoviendo la eficiencia operativa.
Ruta estándar de tareas

La ruta o plan de tareas estandarizadas es un documento consolidado que lista todas las actividades de Mantenimiento que deben realizarse. Este documento se actualiza a medida que avanza en los pasos del Mantenimiento Autónomo y debe revisarse siempre que haya cambios en los equipos o en los planes de mantenimiento. La ruta estándar garantiza que toda la información necesaria para llevar a cabo las tareas esté disponible, proporcionando una guía clara y consistente para los operadores.
Etiquetas para identificación de problemas
Las etiquetas se utilizan para identificar problemas y anomalías encontradas en los equipos. Contienen información como el tipo de problema, el lugar o subconjunto donde ocurre y la identificación del operador responsable. Hay dos categorías de etiquetas: azul y roja. La etiqueta azul se asigna cuando el operador tiene la capacidad para resolver el problema, mientras que la etiqueta roja se utiliza cuando el operador considera que no tiene los recursos necesarios para resolver el problema, pasando al equipo de mantenimiento. Estas etiquetas ayudan en la comunicación y el registro de problemas, facilitando su posterior reparación.

Lección de «Un punto»
La lección de «un punto» o one point lesson es una herramienta que tiene como objetivo proporcionar instrucciones simples, objetivas y de fácil comprensión sobre una tarea específica o la solución adoptada para un problema. Esta lección contiene un texto conciso y directo, permitiendo que otros miembros del equipo puedan aprender y realizar la misma tarea o solución. Además, la lección de «Un punto» se puede aplicar a otros equipos similares, promoviendo la normalización y la difusión del conocimiento técnico.
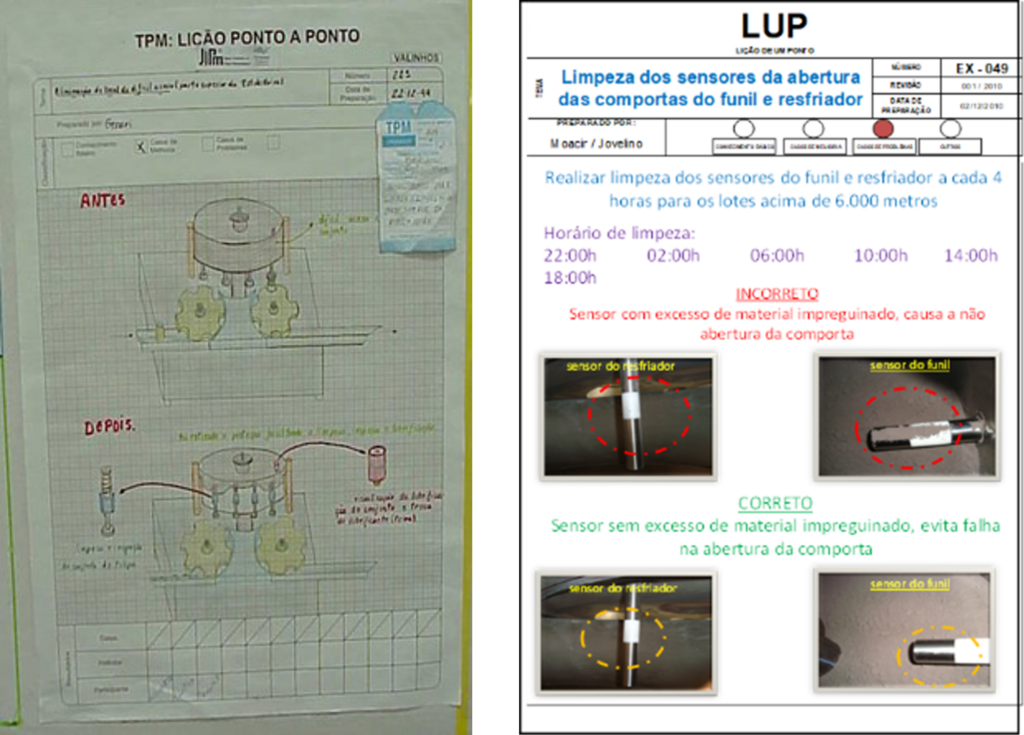
Cuadro de Actividades con Gestión Visual
El cuadro de actividades es un recurso visual que proporciona información actualizada de manera accesible y visible para todos. En él se registran los datos relevantes de las actividades de mantenimiento. Esta pizarra facilita la consulta rápida y el seguimiento de las actividades en tiempo real. Además, las reuniones con el equipo pueden llevarse a cabo frente al cuadro de actividades, promoviendo una toma de decisiones más rápida e informada.


Relación del mantenimiento autónomo con los otros pilares del TPM
El Mantenimiento Autónomo está estrechamente relacionado con los otros pilares del TPM.
Es esencial establecer una buena integración entre los pilares del Mantenimiento Autónomo y el Mantenimiento Planificado, ya que la evolución de la división de tareas de mantenimiento entre los operadores de producción y el equipo de mantenimiento debe coordinarse de manera eficiente. En el caso del pilar de la Mejora Específica, desempeña un papel importante al ayudar a los equipos a resolver los problemas de los equipos trabajando en la causa raíz. Por otro lado, el pilar de la formación y la práctica capacita a los equipos con las habilidades y conocimientos necesarios para desempeñar adecuadamente las nuevas funciones y responsabilidades.
En la siguiente tabla, se pueden ver las actividades de los diferentes pilares que ocurren simultáneamente.
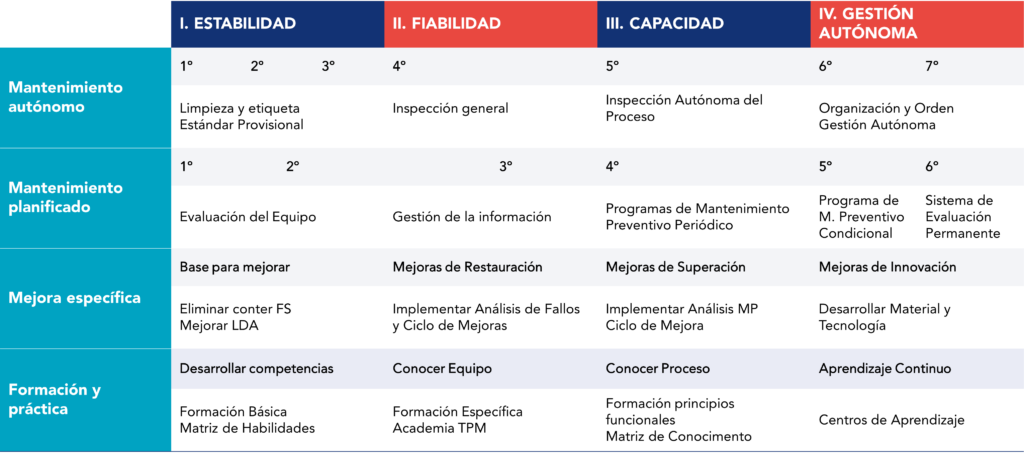